Maintenance methods commonly used in the use of regulating valves
日期:2022-04-14 Click:224
In the modern industrial automation control system, the regulating valve is an indispensable link. Therefore, the normal operation of the regulating valve is related to the guarantee of the quality and output of industrial products. Therefore, the instrument workers in the factory must master the basic electric regulating valve. And the method of repair and maintenance of pneumatic control valve.
Control valves are divided into electric control valves and pneumatic control valves, and there are also hydraulic control valves in a few occasions. There are generally two types of control valve maintenance: one is preventive maintenance, which mainly refers to the preventive maintenance measures taken when there is no fault in order to ensure the reliable operation of the control valve, including a series of measures taken when the control valve is installed and used on site. preventive measures. The second is fault maintenance, that is, a series of maintenance work performed when the regulating valve cannot meet the operating requirements under fault conditions. Generally, it is completed in the production workshop, and may also be directly repaired on the pipeline under special circumstances.
Preventive maintenance: Preventive maintenance is the planned maintenance before the failure of the regulating valve, which can be understood as routine maintenance, which usually includes the following work.
1.1 Stress relief; pipelines will generate various forces due to improper combination or installation, such as thermal stress generated by high-temperature media, stress caused by unbalanced tightening force during installation, and some artificial bumps caused by the regulating valve and its pipelines. stress, etc. These stresses on the control valve and its pipelines can easily affect the performance of the control valve, and in severe cases, it will affect the control valve system itself, resulting in the deformation of the valve stem and the guide, which cannot be aligned with the valve seat; for split valves Therefore, it is necessary to avoid or eliminate stress at any time, and direct the stress away from the regulating valve.
1.2 Check the support; the best position for installing the regulating valve is to make the stroke direction of the valve stem and the actuator above the valve body on a vertical plane. If the regulating valve must be installed in a position where the valve stem can move horizontally or the moving direction of the valve stem has a certain inclination with the horizontal plane, the actuator should be supported so that all parts of the regulating valve are in a natural state. If no support is added or the support is improperly erected, it may cause the valve stem and valve seat of the control valve to be misaligned, which may easily lead to faults such as differential change or leakage of packing. Even if the control valve has fixing and supporting measures, it must be checked regularly. Generally, 2 ~3 monthly inspections.
1.3 To remove or prevent foreign objects from entering, it is necessary to frequently check whether there is rust, welding slag, dirt, etc. in the connecting pipeline of the regulating valve, and should be removed in time after discovery. If foreign matter is easy to accumulate in the control valve and pipeline, consider installing a simple filter device on the downstream side of the control valve. Where hard impurities are likely to penetrate into the process medium, a permanent filter device must be installed. Because when the regulating valve is closed, a small piece of rust or welding slag is enough to damage the well-ground sealing surface, and these dirt also cause wear on the valve core and valve seat of the regulating valve, affecting its normal operation.
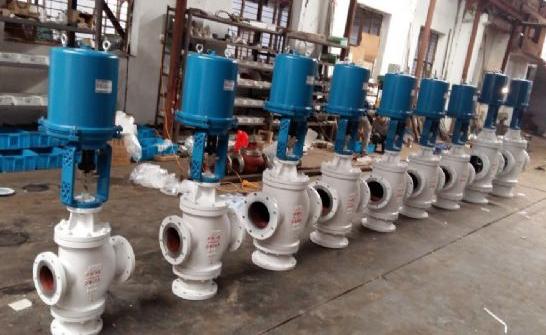
Control valves are divided into electric control valves and pneumatic control valves, and there are also hydraulic control valves in a few occasions. There are generally two types of control valve maintenance: one is preventive maintenance, which mainly refers to the preventive maintenance measures taken when there is no fault in order to ensure the reliable operation of the control valve, including a series of measures taken when the control valve is installed and used on site. preventive measures. The second is fault maintenance, that is, a series of maintenance work performed when the regulating valve cannot meet the operating requirements under fault conditions. Generally, it is completed in the production workshop, and may also be directly repaired on the pipeline under special circumstances.
Preventive maintenance: Preventive maintenance is the planned maintenance before the failure of the regulating valve, which can be understood as routine maintenance, which usually includes the following work.
1.1 Stress relief; pipelines will generate various forces due to improper combination or installation, such as thermal stress generated by high-temperature media, stress caused by unbalanced tightening force during installation, and some artificial bumps caused by the regulating valve and its pipelines. stress, etc. These stresses on the control valve and its pipelines can easily affect the performance of the control valve, and in severe cases, it will affect the control valve system itself, resulting in the deformation of the valve stem and the guide, which cannot be aligned with the valve seat; for split valves Therefore, it is necessary to avoid or eliminate stress at any time, and direct the stress away from the regulating valve.
1.2 Check the support; the best position for installing the regulating valve is to make the stroke direction of the valve stem and the actuator above the valve body on a vertical plane. If the regulating valve must be installed in a position where the valve stem can move horizontally or the moving direction of the valve stem has a certain inclination with the horizontal plane, the actuator should be supported so that all parts of the regulating valve are in a natural state. If no support is added or the support is improperly erected, it may cause the valve stem and valve seat of the control valve to be misaligned, which may easily lead to faults such as differential change or leakage of packing. Even if the control valve has fixing and supporting measures, it must be checked regularly. Generally, 2 ~3 monthly inspections.
1.3 To remove or prevent foreign objects from entering, it is necessary to frequently check whether there is rust, welding slag, dirt, etc. in the connecting pipeline of the regulating valve, and should be removed in time after discovery. If foreign matter is easy to accumulate in the control valve and pipeline, consider installing a simple filter device on the downstream side of the control valve. Where hard impurities are likely to penetrate into the process medium, a permanent filter device must be installed. Because when the regulating valve is closed, a small piece of rust or welding slag is enough to damage the well-ground sealing surface, and these dirt also cause wear on the valve core and valve seat of the regulating valve, affecting its normal operation.