Safety Considerations During Valve Installation
日期:2022-04-14 Click:293
When designing and installing valve piping, the following problems and solutions must be considered:
Valves can leak, either initially or during service, in stuffing box covers, flange gaskets, or when the valve is damaged. It is conceivable that such leaks will develop. If a liquid flows through a valve under very severe operating conditions (high temperature and high pressure), what kind of damage might it experience? Will corrosive fluids collect in cable trays, and flammable liquids fall into hot containers? Will the hot fluid of the alkaline solution harm the operator?
After shutting off, the valve can maintain system pressure for a period of time. If the valve is to be opened or removed for re-service, there must be safety measures to reduce this pressure. Means must also be provided for the discharge of accumulated hazardous liquids.
When designing a valve system, the following points need to be considered:
1. The sealing design of the control valve. Single-seat valves can achieve leaks of less than 1 drop per hour. Double seat valves are difficult to close tightly on both seats. Therefore, the possibility of switching to a single-seat valve must be considered.
2. A large amount of high-pressure fluid accumulated between the shut-off valves may exhibit considerable force, and serious personal accidents may occur if the operation of re-venting the pressure of the control valve is careless.
3. Is the fluid a gas, a clean liquid, or a liquid with suspended solids?
Even with good valve design, high-pressure liquid will inevitably accumulate when it is cut off. Therefore, it is recommended that a vent valve and a drain valve be installed on each side of the control valve if the potential energy of the liquid is very dangerous.
For valves that accumulate large amounts of high-pressure material, consider the reasonableness of installing two vent and discharge valves. Only a small amount of material accumulates between the two valves, while the pressure of the system can be gradually released, allowing the fluid pressure between the two discharge or vent valves to repeatedly build up and discharge. Note that the control valve must be open during this process.
If the fluid being vented is a hazardous gas, the vent line must be connected to a safe place.
If the gas is not flammable, the vent line outlet is still required to avoid rust or other substances being entrained in the blown gas, which could injure those who are handling the vent valve.
Choose a vent valve that will continuously throttle to protect careless operators who fail to follow the safe practice of slowly opening the vent valve. If the fluid contains suspended particles, this restrictive vent valve is prone to clogging. Therefore, it may be necessary to vent from the valve installed at the top of the pipeline, so that a large-sized discharge valve should be used for safe venting. In this regard, it is very important to train personnel on the safe operation of the restrictor vent valve. If the fluid being discharged is a hazardous liquid, the designer of the piping system should consider connecting the discharge line to a safe location. During the operation of the unit, the valve can be very hot, therefore, precautions must be taken to avoid scalding the operator.
Valves can leak, either initially or during service, in stuffing box covers, flange gaskets, or when the valve is damaged. It is conceivable that such leaks will develop. If a liquid flows through a valve under very severe operating conditions (high temperature and high pressure), what kind of damage might it experience? Will corrosive fluids collect in cable trays, and flammable liquids fall into hot containers? Will the hot fluid of the alkaline solution harm the operator?
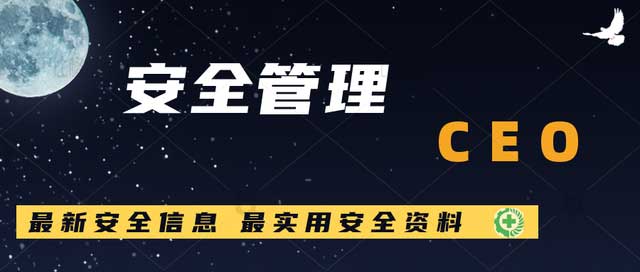
After shutting off, the valve can maintain system pressure for a period of time. If the valve is to be opened or removed for re-service, there must be safety measures to reduce this pressure. Means must also be provided for the discharge of accumulated hazardous liquids.
When designing a valve system, the following points need to be considered:
1. The sealing design of the control valve. Single-seat valves can achieve leaks of less than 1 drop per hour. Double seat valves are difficult to close tightly on both seats. Therefore, the possibility of switching to a single-seat valve must be considered.
2. A large amount of high-pressure fluid accumulated between the shut-off valves may exhibit considerable force, and serious personal accidents may occur if the operation of re-venting the pressure of the control valve is careless.
3. Is the fluid a gas, a clean liquid, or a liquid with suspended solids?
Even with good valve design, high-pressure liquid will inevitably accumulate when it is cut off. Therefore, it is recommended that a vent valve and a drain valve be installed on each side of the control valve if the potential energy of the liquid is very dangerous.
For valves that accumulate large amounts of high-pressure material, consider the reasonableness of installing two vent and discharge valves. Only a small amount of material accumulates between the two valves, while the pressure of the system can be gradually released, allowing the fluid pressure between the two discharge or vent valves to repeatedly build up and discharge. Note that the control valve must be open during this process.
If the fluid being vented is a hazardous gas, the vent line must be connected to a safe place.
If the gas is not flammable, the vent line outlet is still required to avoid rust or other substances being entrained in the blown gas, which could injure those who are handling the vent valve.
Choose a vent valve that will continuously throttle to protect careless operators who fail to follow the safe practice of slowly opening the vent valve. If the fluid contains suspended particles, this restrictive vent valve is prone to clogging. Therefore, it may be necessary to vent from the valve installed at the top of the pipeline, so that a large-sized discharge valve should be used for safe venting. In this regard, it is very important to train personnel on the safe operation of the restrictor vent valve. If the fluid being discharged is a hazardous liquid, the designer of the piping system should consider connecting the discharge line to a safe location. During the operation of the unit, the valve can be very hot, therefore, precautions must be taken to avoid scalding the operator.